A Digital Twin Engineer creates virtual models of physical systems. They use data to simulate and predict system performance.
Digital Twin Engineers are pivotal in the digital transformation era. They develop digital replicas of physical assets, enabling predictive maintenance, real-time monitoring, and optimization of performance. This role involves integrating IoT, data analytics, and machine learning to ensure accurate simulations.
Industries like manufacturing, healthcare, and smart cities benefit immensely from their expertise. These engineers help reduce downtime, enhance efficiency, and drive innovation. As technology advances, the demand for skilled Digital Twin Engineers continues to rise. Their work bridges the gap between the physical and digital worlds, making them indispensable in today’s tech-driven landscape.
Introduction To Digital Twin
The world of technology is ever-evolving. Among the latest innovations is the concept of the Digital Twin. This technology is changing many industries. From manufacturing to healthcare, Digital Twin offers numerous benefits. Let’s dive into understanding this revolutionary concept.
Concept And Definition
A Digital Twin is a virtual model. It replicates a physical object or system. This technology allows for real-time monitoring and analysis. The virtual model updates as the real-world object changes. This helps in improving performance and predicting issues.
- Virtual Model: A digital representation of a physical object.
- Real-time Monitoring: Tracks changes instantly as they happen.
- Predictive Analysis: Helps foresee potential problems.
Historical Background
The concept of Digital Twin has roots in the early 2000s. NASA used it for space exploration missions. They created digital replicas of spacecraft to monitor and manage them. Over time, other industries adopted this technology. Today, it is widely used in manufacturing, healthcare, and smart cities.
- Early 2000s: NASA pioneers the concept.
- Adoption: Other industries begin to use Digital Twin.
- Current Uses: Widely applied in various sectors.
Industry | Application |
---|---|
Manufacturing | Optimize production processes |
Healthcare | Monitor patient health |
Smart Cities | Manage urban infrastructure |
Understanding Digital Twin opens up many possibilities. It can transform how we interact with the physical world. Stay tuned for more insights on this exciting technology!
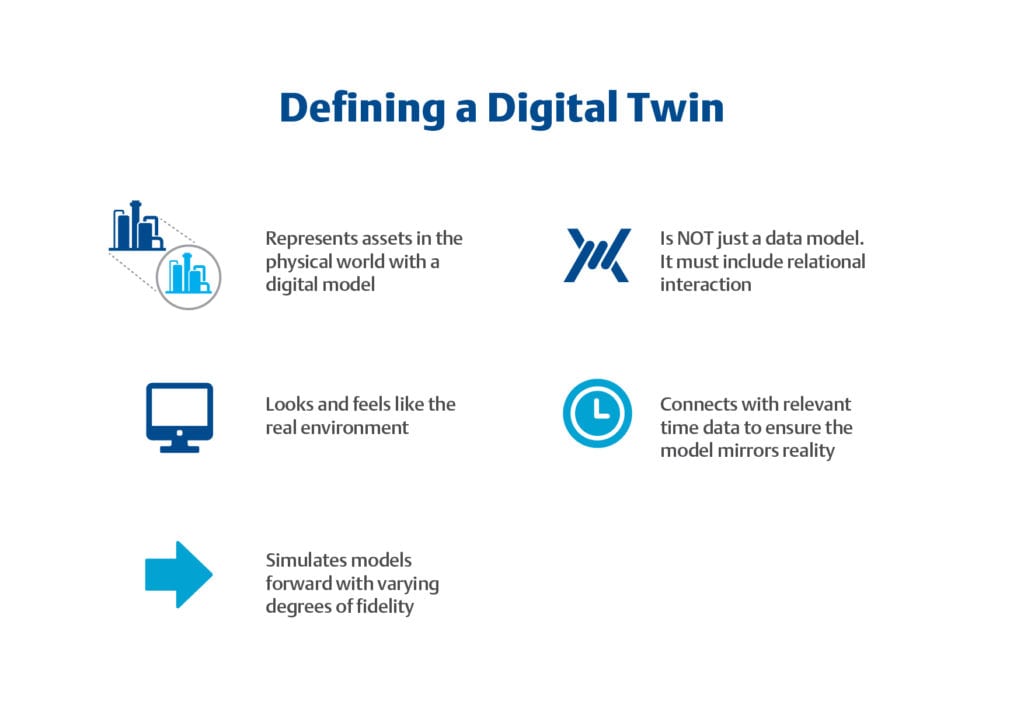
Credit: www.chemengonline.com
Core Technologies
The role of a Digital Twin Engineer revolves around several core technologies. These technologies form the backbone of digital twin systems. Understanding these core technologies is essential for effective digital twin implementation.
Iot Integration
IoT Integration is crucial for digital twins. IoT devices collect real-time data from the physical world. This data feeds into the digital twin system, creating an accurate virtual model. Engineers use this model to monitor and optimize physical assets.
Key aspects of IoT integration include:
- Sensors – Gather data like temperature, pressure, and humidity.
- Connectivity – Use networks like Wi-Fi, Bluetooth, and 5G.
- Data Transmission – Ensure reliable and secure data flow.
Data Analytics
Data Analytics is the brain of digital twins. It processes and analyzes the data collected by IoT devices. This helps in making informed decisions and predictions. Engineers rely on analytics to improve performance and efficiency.
Data analytics involves:
- Data Collection – Gather data from various sources.
- Data Processing – Clean and organize the collected data.
- Data Analysis – Use algorithms to extract meaningful insights.
- Visualization – Present data through graphs and charts.
By mastering IoT integration and data analytics, a Digital Twin Engineer can create powerful digital replicas. These replicas provide valuable insights into the real world.
Applications In Industry 4.0
Digital Twin Engineers are revolutionizing Industry 4.0. They bridge the physical and digital worlds. This technology is transforming various sectors, making processes more efficient and intelligent. Let’s explore its applications in Manufacturing and Supply Chain Management.
Manufacturing
Digital Twins optimize manufacturing processes. They create a virtual replica of physical assets. This allows for real-time monitoring and predictive maintenance. By simulating different scenarios, manufacturers can identify potential issues before they occur. This reduces downtime and increases productivity.
- Real-time Monitoring: Track machine performance and detect anomalies.
- Predictive Maintenance: Schedule repairs before a failure happens.
- Process Optimization: Simulate and improve production workflows.
Digital Twins also help in quality control. They ensure products meet high standards. This leads to fewer defects and higher customer satisfaction.
Supply Chain Management
Digital Twins are transforming supply chains. They provide a comprehensive view of the entire process. This includes everything from raw materials to finished products.
Aspect | Benefit |
---|---|
Inventory Management | Maintain optimal stock levels. |
Logistics Planning | Optimize routes and reduce transportation costs. |
Supplier Coordination | Enhance communication with suppliers. |
With Digital Twins, companies can predict supply chain disruptions. They can develop strategies to mitigate risks. This ensures a smoother and more efficient supply chain.
Role Of A Digital Twin Engineer
The role of a Digital Twin Engineer is essential in modern technology. They create virtual models of physical assets. These models help in monitoring, analyzing, and optimizing performance.
Key Responsibilities
Digital Twin Engineers have many responsibilities. They ensure the digital model matches the physical asset.
- Data Collection: They gather data from physical assets.
- Model Creation: They build accurate digital replicas.
- Simulation: They run simulations to predict outcomes.
- Analysis: They analyze data for insights.
- Optimization: They improve asset performance.
Necessary Skills
Digital Twin Engineers need diverse skills. Here are some key skills:
Skill | Description |
---|---|
Programming | Proficiency in languages like Python and Java. |
Data Analysis | Ability to analyze large datasets. |
3D Modeling | Skills in creating 3D models of assets. |
Problem Solving | Strong analytical and problem-solving skills. |
Communication | Effective communication with team members. |
These skills help Digital Twin Engineers in their daily tasks. They ensure digital twins are accurate and useful.
Benefits For Businesses
Digital Twin Engineers help companies in many ways. They use virtual models of real-world objects or systems. These models bring many advantages. Let’s explore some key benefits.
Cost Efficiency
Businesses save money with digital twin technology. Engineers can test ideas without using real materials. This reduces waste and mistakes. Simulations help find the best way to do things. This saves time and money. Predictive maintenance also lowers costs. Companies fix problems before they become big issues. This means less downtime and fewer repairs.
Improved Productivity
Digital twins boost productivity. They show how systems will work before they are built. This helps teams plan better. Real-time data makes operations smooth. Workers can see problems and fix them fast. Automation becomes easier with digital twins. Machines can talk to each other and work better together. This makes the whole process faster and more efficient.
Benefit | Description |
---|---|
Cost Efficiency | Save money by reducing waste and mistakes. Predictive maintenance cuts repair costs. |
Improved Productivity | Plan better and fix problems quickly. Automation increases speed and efficiency. |
Challenges And Solutions
Digital Twin Engineers face unique challenges. These challenges can affect efficiency and security. Let’s explore some common challenges and their solutions.
Data Security
Digital Twin technology relies on large volumes of data. This data includes sensitive information. Protecting this data is crucial.
Encryption is one key solution. Encrypting data ensures only authorized users can access it. Another solution is multi-factor authentication. This adds an extra layer of security.
Regular security audits can help identify vulnerabilities. These audits should be performed by experts. Security protocols should be updated regularly.
Interoperability
Digital Twin systems often integrate with various technologies. Ensuring these systems work together seamlessly is a challenge.
One solution is using standardized communication protocols. These protocols ensure different systems can communicate effectively. Another approach is modular system design. This allows for easy integration and updates.
Providing comprehensive documentation can also aid interoperability. This documentation should include detailed integration guides. Training sessions for engineers can further enhance system compatibility.
Future Trends
The world of Digital Twin Engineering is constantly evolving. Future trends in this field promise to revolutionize industries. Key areas to watch include AI integration and scalability. These trends will shape the future of digital twins and their applications.
Ai Integration
AI integration is set to transform digital twin engineering. Artificial Intelligence helps in creating more accurate and dynamic models. AI algorithms can analyze massive amounts of data quickly. This leads to better decision-making and predictive maintenance.
With AI, digital twins can learn from historical data. They can also adapt to new information in real-time. This makes them more efficient and reliable. Industries like manufacturing and healthcare will benefit greatly from this integration.
Scalability
Scalability is another critical trend in digital twin engineering. As businesses grow, their digital twin systems need to scale accordingly. This ensures that they can handle increased data and complexity.
Cloud computing plays a vital role in scalability. It allows for flexible and cost-effective expansion. Companies can store and process large amounts of data without significant investments in infrastructure.
Scalability also enables better collaboration among teams. With cloud-based digital twins, multiple users can access and update models simultaneously. This improves efficiency and reduces errors.
Future Trend | Impact |
---|---|
AI Integration | More accurate models, better decision-making, predictive maintenance |
Scalability | Handles increased data, flexible expansion, improved collaboration |
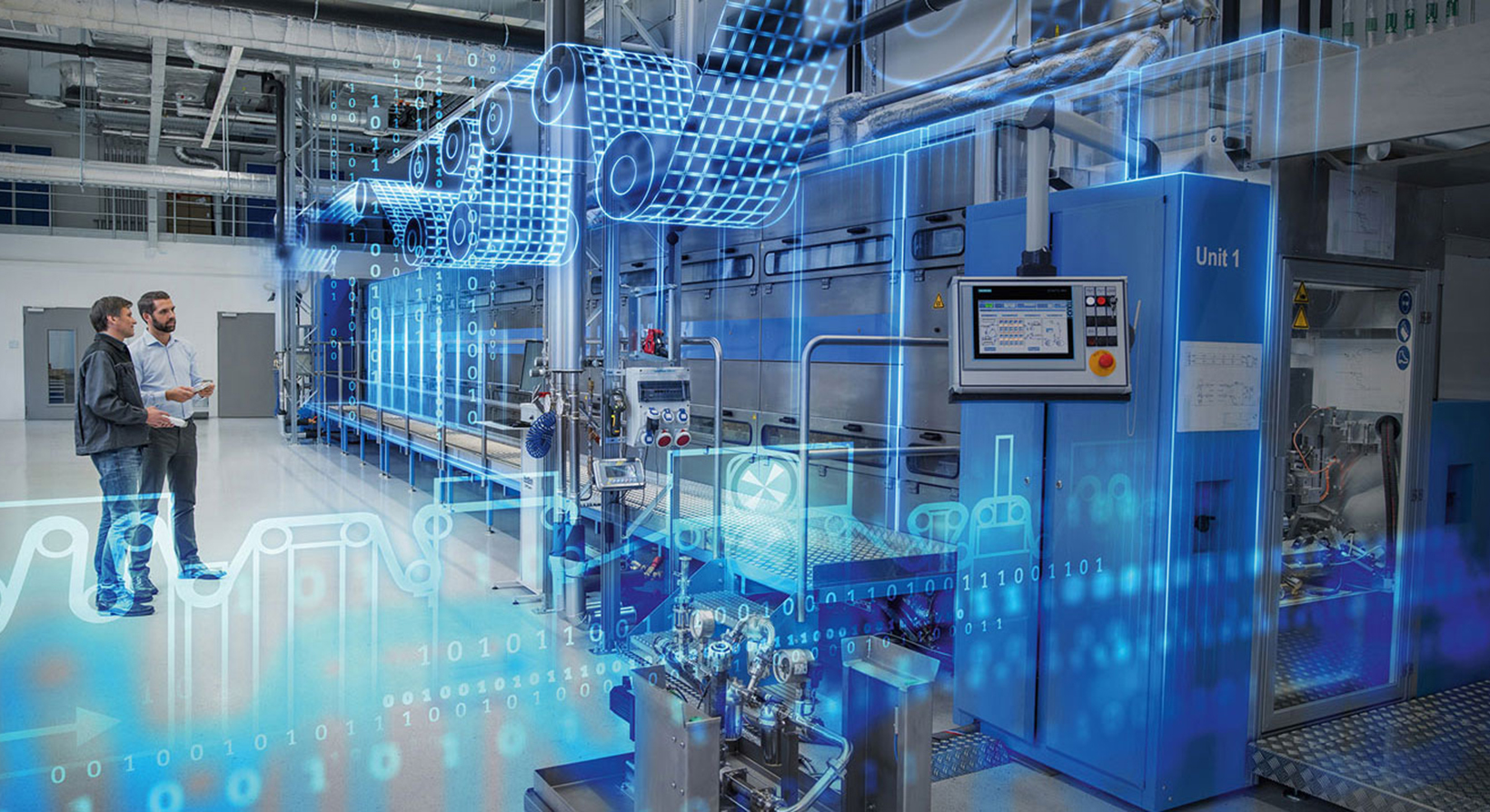
Credit: www.stambol.com
Case Studies
Case studies demonstrate the practical applications of Digital Twin Engineers. These examples show their impact across various industries. Here, we explore two pivotal sectors: Automotive and Healthcare.
Automotive Industry
The automotive industry benefits greatly from Digital Twin technology. Engineers create virtual replicas of vehicles. This allows them to test different scenarios without physical prototypes.
For example, a major car manufacturer reduced development time. They used digital twins to simulate road conditions. This led to quicker design iterations and better safety features.
- Reduces the need for physical prototypes
- Enhances vehicle safety features
- Speeds up the development process
Digital twins also help in predictive maintenance. Engineers can monitor vehicle performance in real-time. This reduces downtime and improves customer satisfaction.
In a recent project, a company cut maintenance costs by 20%. They used digital twins to predict part failures. This proactive approach saved millions.
Healthcare Sector
The healthcare sector also sees significant improvements with Digital Twin technology. Medical professionals use virtual models of patients. This helps in personalized treatment plans and better outcomes.
For instance, surgeons can practice complex procedures on digital twins. This increases the success rate of surgeries. It also reduces patient risk.
- Enables personalized treatment plans
- Improves surgical success rates
- Reduces patient risk
A hospital implemented digital twin technology to monitor patient vitals. This led to early detection of health issues. As a result, patient recovery times improved by 15%.
Another case study shows a biotech firm using digital twins. They accelerated drug development. This allowed them to bring new medicines to market faster.
Industry | Benefit | Result |
---|---|---|
Automotive | Quicker design iterations | Enhanced safety features |
Healthcare | Personalized treatment plans | Improved patient outcomes |

Credit: imr.ie
Frequently Asked Questions
What Is A Digital Twin Engineer?
A digital twin engineer creates virtual models of physical systems. They simulate, analyze, and optimize real-world operations for better performance.
Is Digital Twin A Good Career?
Yes, a digital twin career is promising. It offers high demand, competitive salaries, and opportunities in various industries, including healthcare, manufacturing, and smart cities.
Does Digital Twin Require Coding?
Yes, creating a digital twin often requires coding. Developers use programming to simulate physical assets accurately.
What Is A Digital Twin Technology?
Digital twin technology creates a virtual replica of physical assets. It helps monitor, analyze, and optimize performance. This technology enhances decision-making and predictive maintenance.
Conclusion
A Digital Twin Engineer plays a vital role in bridging the physical and digital worlds. Their expertise ensures seamless integration and improved efficiency. Embrace this innovative technology to stay ahead in the competitive market. Invest in skilled professionals to drive your business towards a more connected and intelligent future.