Factory automation improves efficiency and reduces human error in manufacturing processes. It involves integrating machines, control systems, and information technologies.
Factory automation transforms traditional manufacturing by leveraging advanced technologies. Automated systems enhance productivity, ensuring consistent quality. Robots, sensors, and software streamline operations, reducing labor costs. Factories become more flexible, adapting quickly to market demands. Automation also enhances worker safety by handling hazardous tasks.
Data analytics play a crucial role, offering insights for continuous improvement. Smart factories utilize IoT, AI, and machine learning for optimal performance. Investing in automation leads to significant long-term savings. Businesses gain a competitive edge through faster production and reduced downtime. Embracing factory automation is essential for modern manufacturing success.
Introduction To Factory Automation
Factory automation is changing how products are made. It involves using technology to control production. This process reduces human effort. Automation brings precision, speed, and efficiency. Many factories now rely on automated systems.
The Rise Of Industrial Automation
Industrial automation started in the late 20th century. Factories began using machines for repetitive tasks. Early automation was simple. Today, it’s highly advanced. Machines can work 24/7 without breaks. They follow programmed instructions perfectly. This rise has transformed manufacturing industries worldwide.
Key Benefits For Manufacturers
Automation offers many benefits to manufacturers. Let’s explore some key advantages:
- Increased Productivity: Machines work faster than humans. They produce more in less time.
- Consistency: Automated systems maintain high-quality standards. Every product is identical.
- Cost Savings: Less human labor means lower costs. Maintenance of machines is also cost-effective.
- Safety: Automation reduces human involvement in dangerous tasks. This improves workplace safety.
Here is a table summarizing these benefits:
Benefit | Description |
---|---|
Increased Productivity | Machines work faster and produce more. |
Consistency | High-quality standards with identical products. |
Cost Savings | Reduced labor and maintenance costs. |
Safety | Less human involvement in dangerous tasks. |
Automation is the future of manufacturing. It’s transforming industries globally. Understanding its benefits is crucial for staying competitive.
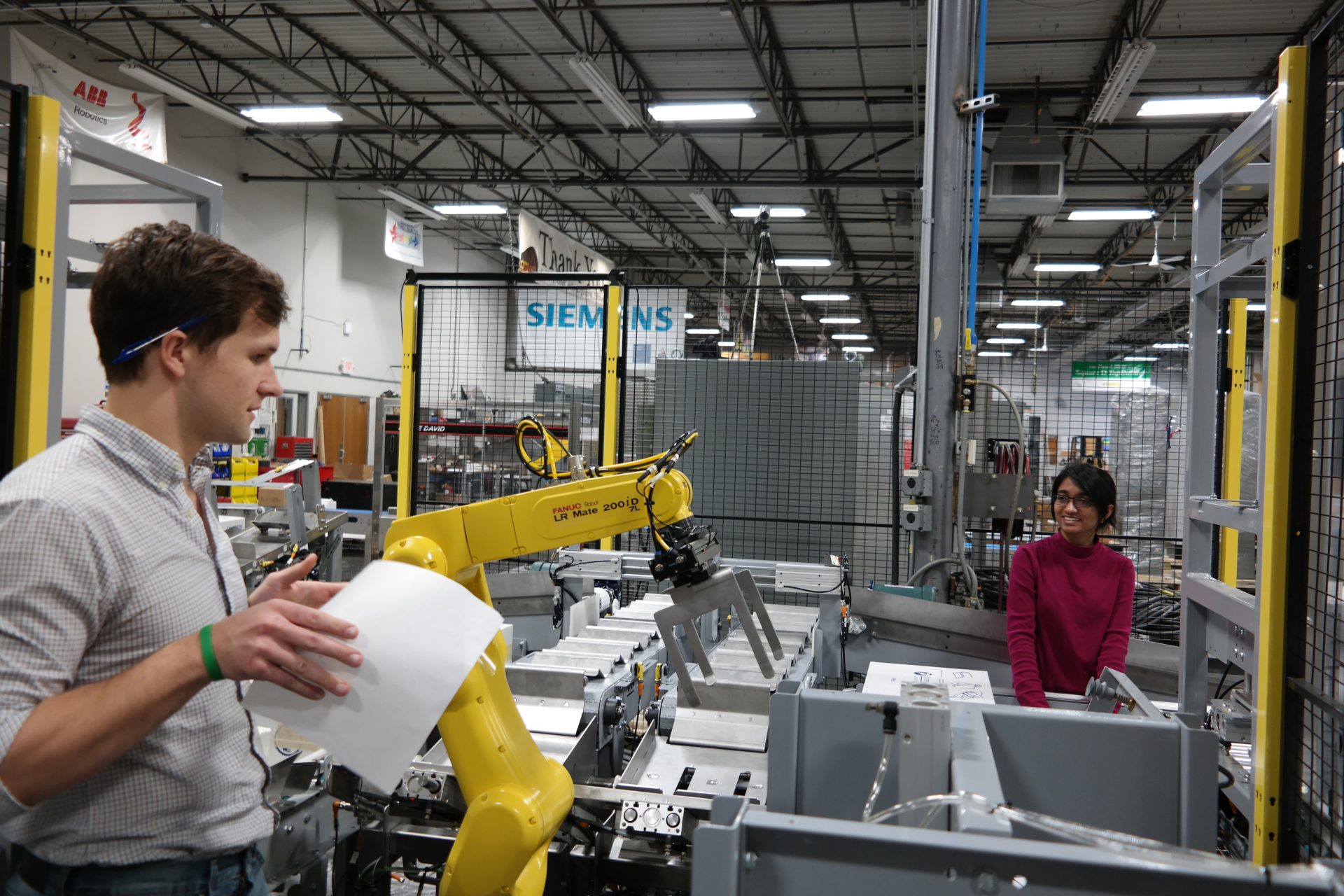
Credit: www.factoryautomation.com
Core Technologies Driving Automation
Factory automation is transforming industries. It boosts efficiency and reduces errors. Core technologies like robotics and AI lead this change. These innovations reshape how factories operate.
Robotics And Cobots In Action
Robots perform repetitive tasks faster than humans. They assemble products, handle materials, and work tirelessly. This improves productivity and reduces human error.
Cobots, or collaborative robots, work alongside humans. They are safe and user-friendly. Cobots can handle complex tasks with human guidance. This collaboration increases flexibility.
Here is a comparison between robots and cobots:
Feature | Robots | Cobots |
---|---|---|
Speed | High | Moderate |
Safety | Requires safeguards | Built-in safety features |
Flexibility | Low | High |
The Role Of Artificial Intelligence
Artificial Intelligence (AI) powers smart factories. AI analyzes data to make decisions. It predicts maintenance needs and optimizes production.
AI systems learn from data. They adapt to changes in real-time. This reduces downtime and improves efficiency.
Here are some key uses of AI in automation:
- Predictive maintenance
- Quality control
- Supply chain optimization
AI also enhances machine learning. Machines learn from experience without explicit programming. This makes them smarter and more efficient over time.
Integration Of Iot In Manufacturing
The Internet of Things (IoT) is revolutionizing the manufacturing sector. It connects devices and systems to each other. This integration allows for seamless communication and data exchange. Factories today are smarter and more efficient due to IoT.
Real-time Data For Decision Making
IoT devices collect real-time data from factory equipment. This data is sent to central systems for analysis. Managers can make informed decisions quickly. They can monitor production lines and detect issues early.
Here are some benefits of real-time data:
- Quick response to problems
- Improved product quality
- Reduced waste and costs
Real-time data helps in optimizing factory operations. It also aids in maintaining product standards and consistency.
Predictive Maintenance And Efficiency
Predictive maintenance is another key benefit of IoT in manufacturing. Sensors on machines predict wear and tear. They alert managers before failures occur.
This approach reduces unplanned downtime. It also extends the lifespan of equipment.
Traditional Maintenance | Predictive Maintenance |
---|---|
Scheduled checks | Condition-based checks |
Frequent replacements | Optimized parts usage |
Higher costs | Lower costs |
Factories also benefit from increased efficiency. IoT enables better resource management. It ensures optimal use of materials and energy.
Here are some key points:
- Lower operational costs
- Increased production speed
- Higher overall efficiency
Predictive maintenance and efficiency improvements are vital. They make factories more competitive in the global market.
Impact On Workforce Dynamics
The shift towards factory automation significantly changes workforce dynamics. Automation brings new opportunities and challenges for employees. Let’s explore how these changes impact workforce dynamics.
Changing Skill Sets And Training
Factory automation requires workers to learn new skills. Traditional tasks are now automated, reducing the need for manual labor. Employees must adapt to new technologies and systems. They need training in robotics, programming, and data analysis.
Companies invest in continuous training programs. These programs help workers stay updated with the latest tools. They also focus on problem-solving and critical thinking skills. This creates a more skilled and adaptable workforce.
Human-robot Collaboration
Automation fosters collaboration between humans and robots. Robots handle repetitive and dangerous tasks. This allows humans to focus on creative and complex work. Collaborative robots, or cobots, work alongside humans.
Cobots enhance productivity and safety. They reduce the physical strain on human workers. This collaboration leads to a more efficient and harmonious work environment.
Here are some benefits of human-robot collaboration:
- Increased productivity
- Improved safety
- Reduced physical strain
- Enhanced job satisfaction
Benefit | Description |
---|---|
Increased Productivity | Robots handle repetitive tasks, speeding up production. |
Improved Safety | Robots perform dangerous tasks, reducing workplace injuries. |
Reduced Physical Strain | Robots assist with heavy lifting, easing physical demands on workers. |
Enhanced Job Satisfaction | Workers focus on more engaging and creative tasks. |
Enhancing Quality Control
Factory automation is revolutionizing quality control in manufacturing. Automated systems ensure products are made to exact specifications. This reduces waste and improves efficiency. Below, we explore how automation enhances quality control.
Precision And Consistency
Automated systems offer unmatched precision and consistency. Machines perform the same task in the same way every time. This ensures each product meets quality standards.
- Robots can measure materials to the micrometer.
- Consistent operations reduce variations in product quality.
Machines work tirelessly without breaks. This leads to uniformity across production batches. Automated systems are programmed to detect even minor defects. They remove defective items before they reach customers.
Manual Process | Automated Process |
---|---|
Inconsistent results | Uniform quality |
Human errors | High precision |
Time-consuming checks | Continuous monitoring |
Reducing Human Error
Automation significantly reduces human error. Humans can make mistakes due to fatigue or distraction. Machines do not face these issues.
- Automated systems follow programmed instructions exactly.
- They do not deviate from set parameters.
Reducing human error leads to higher product quality. This builds customer trust and increases brand reputation. Automated quality control systems can work round the clock. They provide a consistent output without the need for breaks.
Automation also collects data on production processes. This data helps in identifying and correcting issues quickly. It ensures continuous improvement in product quality.
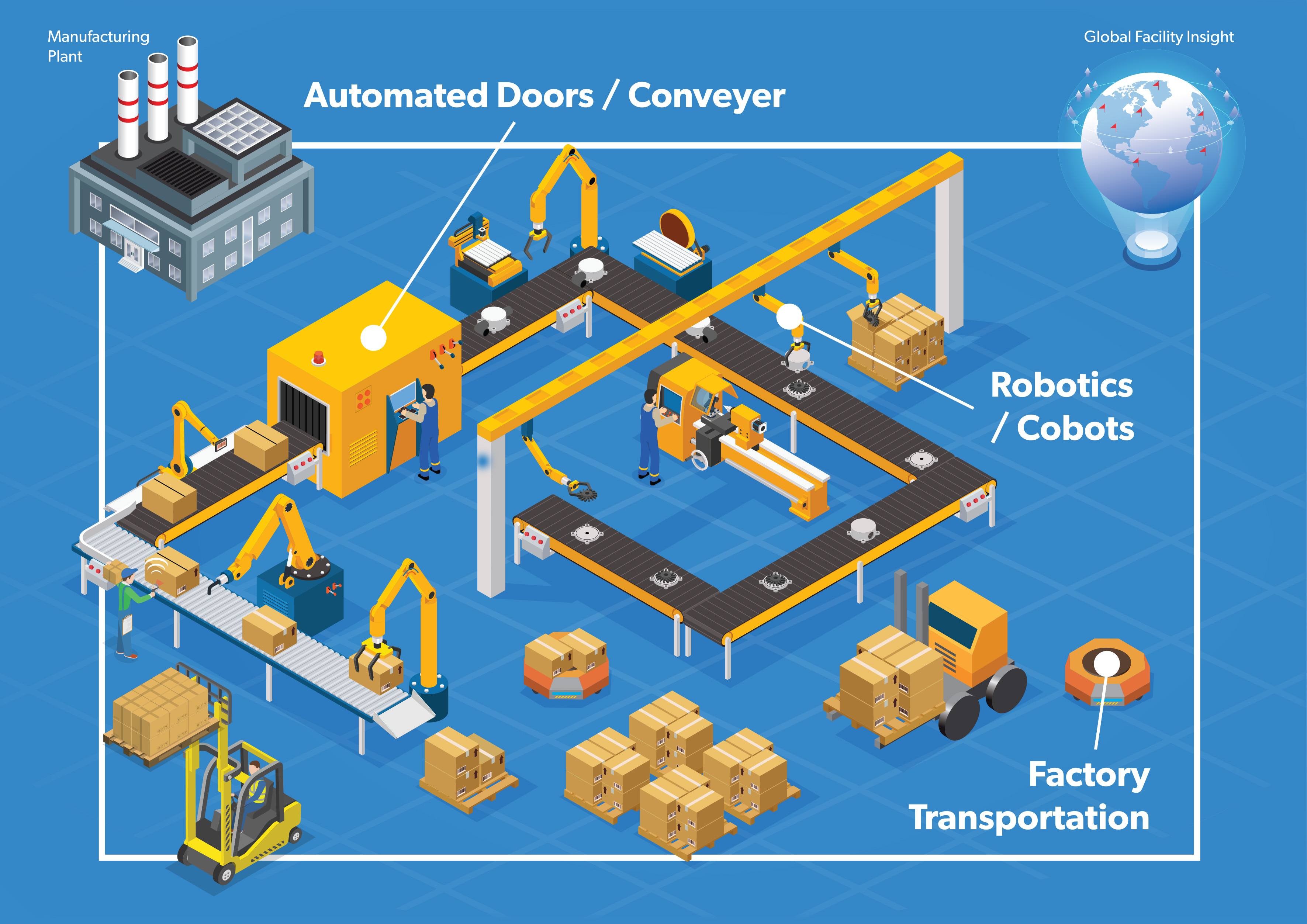
Credit: www.allegromicro.com
Economic Implications Of Automation
Factory automation has a significant impact on the economy. This technology changes how businesses operate. It influences costs, investments, and profits.
Cost Savings And Investment
Factory automation can lead to substantial cost savings. Businesses spend less on labor and reduce errors. Automated systems work faster and more accurately. This efficiency translates into lower production costs.
Initial investment in automation can be high. Companies need to buy machines and software. Training staff is also necessary. Despite the high upfront cost, the long-term savings justify the investment.
Cost Element | Manual | Automated |
---|---|---|
Labor Costs | High | Low |
Error Rate | High | Low |
Production Speed | Slow | Fast |
Long-term Profitability
Automation enhances long-term profitability. Automated systems increase production rates. They also maintain consistent quality. This reliability leads to higher customer satisfaction.
Automated factories can quickly adapt to market changes. They can introduce new products without major disruptions. This flexibility is crucial in a competitive market.
- Higher production rates
- Consistent product quality
- Quick adaptation to market changes
Automation also reduces downtime. Machines can work continuously, unlike human workers. This constant operation increases overall output and revenue.
- Reduced downtime
- Continuous operation
- Increased output
Case Studies: Success Stories
Factory automation is changing businesses in amazing ways. This section will highlight real-world examples. Learn how small businesses and large industries have transformed. These stories showcase the power of automation. They offer insights and inspiration for others.
Small Businesses Transforming
Small businesses often face resource constraints. Automation can be a game-changer. For example, a local bakery automated its packaging process. This reduced labor costs and increased productivity. The bakery saw a 30% rise in output. They also improved product consistency.
Another example is a small electronics shop. They implemented robotic arms for assembly. This cut down errors by 50%. Their customer satisfaction rates soared. Automation allowed them to compete with larger retailers.
Here’s a quick comparison before and after automation:
Metric | Before Automation | After Automation |
---|---|---|
Production Time | 5 hours | 3 hours |
Error Rate | 10% | 5% |
Customer Satisfaction | 70% | 95% |
Large Scale Industrial Turnarounds
Large industries also benefit from automation. A car manufacturing plant automated its paint shop. This reduced waste and improved paint quality. The plant saved millions in materials. They also cut down on manual labor injuries.
Another case is a chemical plant. They installed automated sensors and controls. This improved safety and efficiency. They reduced downtime by 40%. Their profits increased significantly.
Key benefits observed:
- Improved product quality
- Reduced operational costs
- Enhanced worker safety
- Increased production speed
These success stories show the potential of factory automation. Both small and large businesses can thrive with the right technology.
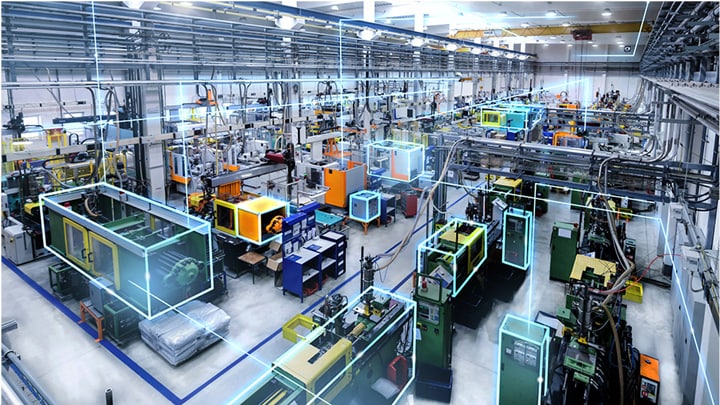
Credit: www.nxp.com
Challenges And Considerations
Factory automation is transforming how industries operate. But it comes with its own set of challenges and considerations. Understanding these challenges can help businesses make informed decisions.
Initial Costs And Roi
One of the first considerations is the initial cost. Setting up an automated system is often expensive. This includes the cost of machinery, software, and installation.
To better understand the costs, let’s look at a simple table:
Expense | Cost |
---|---|
Machinery | $100,000 |
Software | $50,000 |
Installation | $20,000 |
Beyond initial costs, businesses must also consider the Return on Investment (ROI). ROI is crucial in justifying the high initial expenses. Automated systems often lead to increased efficiency and reduced labor costs. This can result in significant savings over time.
Adapting To Technological Changes
Another challenge is keeping up with technological changes. Technology evolves rapidly. Staying updated is essential for maintaining competitiveness.
To adapt effectively, businesses should:
- Invest in regular training for employees.
- Keep software and hardware updated.
- Monitor industry trends and innovations.
Adapting to these changes can be challenging. But it is necessary for long-term success. A proactive approach can make a significant difference.
The Future Of Factory Automation
The future of factory automation is bright and transformative. Advances in technology are rapidly reshaping manufacturing. Factories are becoming smarter and more efficient. Automation is helping companies stay competitive. Let’s explore the emerging trends and innovations, and global market projections.
Emerging Trends And Innovations
Factory automation is evolving with several key trends. Artificial Intelligence (AI) and Machine Learning (ML) are leading the way. These technologies enable machines to learn and adapt. They improve efficiency and reduce errors.
Robotics is another significant trend. Advanced robots can perform complex tasks with precision. They work alongside humans to boost productivity. Collaborative robots (cobots) are designed to be safe and intuitive.
Internet of Things (IoT) is revolutionizing factory operations. IoT devices collect and share data in real-time. This connectivity enhances decision-making and maintenance.
Here are some emerging technologies in factory automation:
- AI and ML
- Robotics
- IoT
- 5G Connectivity
- Digital Twins
Global Market Projections
The global market for factory automation is expanding. It is projected to grow significantly in the coming years. The demand for automation solutions is increasing across industries.
Here are some key market projections:
Region | Market Size (2025) | Growth Rate |
---|---|---|
North America | $45 billion | 8% |
Europe | $50 billion | 7% |
Asia-Pacific | $70 billion | 10% |
Rest of the World | $20 billion | 6% |
These projections highlight the growing importance of automation. Businesses are investing in advanced technologies to stay ahead.
Adopting factory automation leads to several benefits:
- Increased productivity
- Reduced operational costs
- Enhanced product quality
- Improved safety
- Greater flexibility
Automation is not just a trend; it is the future of manufacturing. Companies that embrace these changes will thrive in the competitive landscape.
Frequently Asked Questions
What Is Factory Automation?
Factory automation involves using technology to automate manufacturing processes. It enhances efficiency, reduces human error, and lowers production costs.
How Does Factory Automation Work?
Factory automation uses robotics, control systems, and software. These components work together to perform repetitive tasks efficiently.
What Are The Benefits Of Factory Automation?
Factory automation increases production speed, improves product quality, and reduces labor costs. It also enhances workplace safety.
Can Small Businesses Implement Factory Automation?
Yes, small businesses can implement factory automation. Scalable solutions are available to fit various budgets and needs.
Conclusion
Factory automation is transforming industries, enhancing efficiency, and reducing costs. Businesses adopting automation gain a competitive edge. Embrace factory automation to stay ahead in the fast-evolving market. Invest in advanced technologies for sustainable growth and increased productivity. The future of manufacturing lies in smart, automated solutions.